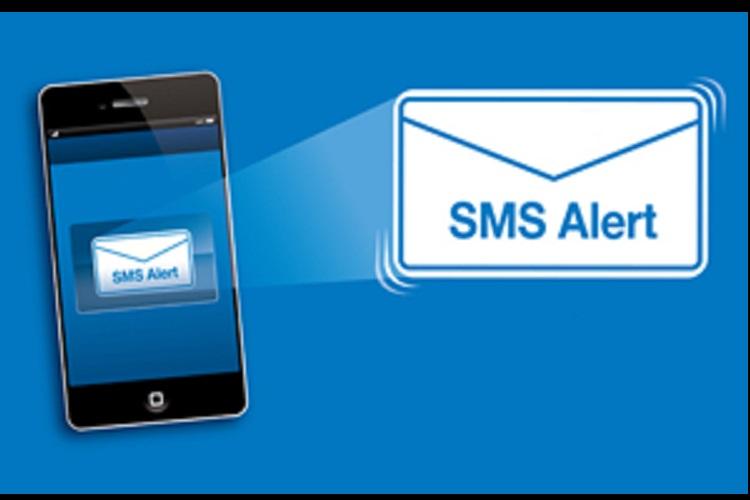
How SequelAlert Helped a Manufacturing Company Avoid Downtime
In the manufacturing industry, efficiency and uptime are crucial for maintaining productivity and profitability. A leading manufacturing company recently implemented an emergency SMS alert system using SequelAlert to enhance their operational reliability and minimize downtime. Faced with the challenges of equipment failures and communication delays, the organization recognized the need for a robust alerting system that could deliver real-time notifications to their maintenance and operations teams.
Before adopting SequelAlert, the company struggled with traditional communication methods that relied on email and internal messaging. These methods often led to delayed responses when equipment issues arose, resulting in costly downtime that affected production schedules. Understanding the urgent need for a more effective solution, the manufacturing company turned to SequelAlert to streamline their incident response and ensure critical alerts reached the right personnel instantly.
This article explores how the implementation of SequelAlert enabled the manufacturing company to avoid significant downtime, enhancing their operational efficiency and overall productivity.
Identifying the Challenges
The manufacturing company faced several challenges with their existing alerting system. Equipment malfunctions could occur at any time, and delays in notifying the maintenance team often resulted in prolonged outages. Without immediate communication, critical issues could escalate, leading to costly production delays and strained relationships with clients.
Recognizing that quick response times were essential for minimizing downtime, the company sought a solution that could provide immediate alerts to maintenance personnel, regardless of their location on the factory floor. This requirement led them to SequelAlert, which offered a powerful emergency SMS alert system designed to meet the demands of fast-paced manufacturing environments.
Implementing SequelAlert
After selecting SequelAlert, the manufacturing company began the implementation process by customizing the system to fit their specific operational needs. They established various alert categories, including equipment failures, maintenance reminders, and safety notifications. This categorization allowed them to prioritize alerts based on urgency, ensuring that critical issues were addressed swiftly.
The integration process involved setting up recipient groups based on roles within the maintenance and operations teams. By leveraging SequelAlert’s capabilities, the company ensured that alerts were clear, actionable, and directed to the appropriate individuals without delay. This targeted approach minimized confusion and ensured that everyone knew their responsibilities during critical incidents.
Training and Engagement
To maximize the effectiveness of SequelAlert, the manufacturing company invested in training for their staff. They organized training sessions to familiarize team members with the new alerting system, emphasizing the importance of prompt responses to SMS notifications. Engaging employees in the training process fostered a culture of accountability and helped ensure everyone was prepared to act quickly during emergencies.
Additionally, the company encouraged feedback from staff during the training sessions, allowing them to voice concerns and suggest improvements. This proactive approach helped enhance the overall adoption of the emergency SMS alert system, ensuring that team members felt confident and capable of utilizing the tool effectively.
Results and Impact
Following the implementation of SequelAlert, the manufacturing company experienced significant improvements in their incident management. Alerts were delivered instantly to the mobile devices of maintenance personnel, allowing for rapid action in response to equipment issues. This capability proved invaluable during critical situations, where quick intervention was essential to prevent prolonged downtime.
The organization reported a marked decrease in incident resolution times, as maintenance staff could now respond to alerts in real time. The streamlined communication facilitated by the emergency SMS alert system empowered team members to focus on resolving issues quickly, ultimately improving operational efficiency and production output.
Continuous Improvement
Recognizing the importance of continuous improvement, the manufacturing company established a framework for regularly assessing the effectiveness of SequelAlert. They conducted periodic reviews of alert configurations, response times, and overall system performance. This commitment to ongoing evaluation ensured that the alerting system remained aligned with the evolving needs of the organization.
Looking ahead, the company plans to further integrate SequelAlert with their existing maintenance management systems to create a more comprehensive incident management ecosystem. By leveraging analytics and reporting capabilities, they aim to refine their alerting processes and enhance their responsiveness to emerging challenges in the manufacturing sector.
Conclusion
The successful implementation of SequelAlert as an emergency SMS alert system has transformed the way the manufacturing company manages its operations. By streamlining communication, improving incident response times, and fostering a culture of accountability, the organization significantly enhanced its operational efficiency and minimized downtime.
As the manufacturing industry continues to evolve, investing in robust alerting systems like SequelAlert is essential for ensuring that critical information reaches the right people at the right time, ultimately driving productivity and maintaining competitive advantage.